The advancement of 3-D printing could change the way products are made. And, in an increasingly eco-conscious world, consumers want products that they know were made sustainably, but also of high quality.
Researchers have developed a method of 3-D printing using wood scraps to create new wooden products that look and feel like products made with lumber straight from the woods. It’s all part of a larger effort to minimize scrap wood, of which the U.S. produces about 18 million tons a year, with more than 12 million of that ending up in landfills.
Scientific American detailed the new process like this:
Natural wood is made up mostly of organic polymers called cellulose and lignin, along with smaller amounts of pectin, wax and other compounds. To convert wood scraps into ink for 3D printing, the researchers started by combining just lignin and cellulose, keeping the ratio of these materials the same as that found in natural wood. For this part of the process […] any kind of wood or wood waste can be used.
This differs from previous 3-D printing processes involving wood. In the past, sawdust was mixed with a binding agent to form a “wood-like composite” that didn’t have the natural look, feel or strength of a true wooden product. Researchers added that it doesn’t necessarily need to be wood. Any plant that has lignin and cellulose would work.
Researchers at Rice University created miniature furniture, a honeycomb lattice and alphabetical letters.
The goal here for the researchers at Rice University was to make a product that served as a solid stand-in for wood.
“The ability to create a wood structure directly from its own natural components sets the stage for a more eco-friendly and innovative future,” Muhammad Rahman, an assistant research professor of materials science and nanoengineering at Rice University, said in a statement. “It heralds a new era of sustainable 3D-printed wood construction.”
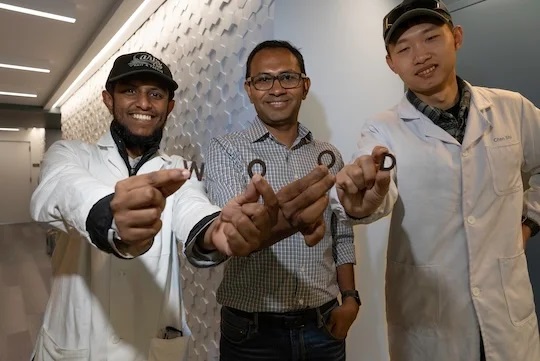
One of the key issues researchers dealt with was creating a wooden ink that had the right “flow,” which they called rheology. This involved trial and error with two different forms of cellulose: nanofibers and crystals.
“If you use more nanofiber than nanocrystal, you get chunky globules that you cannot print, or you need very high pressures to print that,” Rahman told Scientific American.
Furthering the environmentalism of it all, the researchers did not use any synthetic additives which are commonly used in current wood printing processes. That way, the ink and printed products could be recycled in this same way.
When the printed products were air dried, the researchers found that they’d end up deformed. To maintain the shape, they freeze-dried them at -112 degrees Fahrenheit in a vacuum, and then were heated to 356 degrees Fahrenheit to soften the lignin and allow it to bind more effectively.
The researchers found that the products had similar attributes to natural hardwood and were optimistic about being able to take this idea even further to “surpass the properties of hardwood,” such as making them fire-resistant, Rahman said.
Whether this replaces, complements or even affects the current wood product market remains to be seen. As it stands, it involves a lot of processes that typical 3-D printing or woodworking do not require. But, again, as manufacturers and consumers alike are looking for more sustainable products, this has potential if it were to become easier and more ubiquitous down the road – especially if it becomes cost efficient compared to natural wood processing.
Rahman and the team believe that further tweaks in the ink could result in quicker printing times, which would appeal to manufacturers.